轴承是在机械传动过程中起固定和减小载荷摩擦系数作用的部件,广泛应用于各种机械装备上,轴承质量的好坏严重影响整个机械设备的运行稳定性。但在轴承生产、装配的过程中,由于加工技术和微小异物的因素,导致生产的轴承表面产生一些缺陷。常见缺陷种类包括裂纹、黑斑、锈蚀、凹坑、划痕、缺盖、浮盖以及倒角不均匀等。这些缺陷不仅影响轴承产品的外观,也严重影响轴承的性能。宁波市作为我国轴承生产基地之一,轴承企业约有1000多家,仅慈溪进出口公司出口的轴承就占全国轴承出口总量的10%,轴承已经成为宁波重要的出口创汇产品。近年来,各生产企业通过技术改造,在生产上采用了自动化单机或自动化生产线,但对于缺陷轴承检测和分拣仍采用人工目测的方式,这样不仅工作量大、效率低,而且漏检率高,严重影响产品出厂效率,与自动化加工线极不相称。不仅给企业造成了经济损失,而且带来了负面影响,使企业信誉受到损害。因此企业急需一种自动化轴承缺陷检测设备以弥补人工分拣的短板。
实验室针对宁波市轴承生产行业面临的高速自动化生产模式和低效率高成本的人工目测缺陷分拣的高度差异现状,旨在开发一套配合自动化加工生产线的轴承缺陷检测系统,替代现有的人工目测方式,提升轴承分拣的效率和精度,研究并攻克了以下关键技术:(1)设计并搭建视觉采集方案,包括各检测工位的光源、相机的选型、安装方式、光源频闪及同步采集技术。(2)设计并搭建轴承缺陷检测系统中的机械传动模块,包括上料装置、输送装置、轴承翻转装置、分拣装置,整体运行通过PLC控制协调。(3)设计基于混合注意力机制的YOLOV4网络的缺陷检测算法,保证缺陷检测的鲁棒性和实时性。(4)开发轴承检测系统的软件,包括缺陷检测、PC与PLC之间的串行通讯、光源和相机配置、算法调试以及检测结果统计和实时显示。研制开发的系统达到以下技术指标:缺陷检出率: 96.9%;误检率: 2%;检测效率< 2秒/个;可检测缺陷种类>10种。
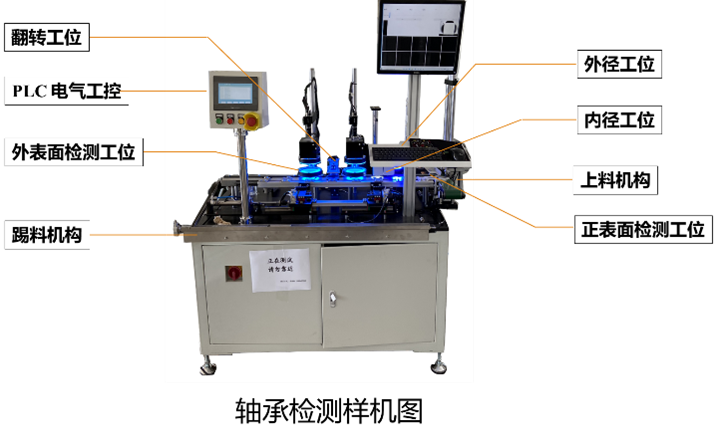
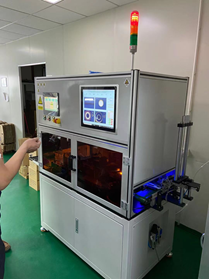
研制的轴承表面缺陷自动全检测系统
|